Análisis de riesgos, ¿Cuándo ocurrirá un incidente? ¿Qué hacer cuando ocurra? ¿Cómo prevenir el incidente? Muchas dudas difíciles de conocer cómo prevenir y estar listos para cuando ocurran se realizan, los accidentes están al día, es decir, pueden ocurrir sin avisar en cualquier segundo, pueden ser accidentes menores y accidentes fatales, todo en medida de cómo se traten las medidas de seguridad, pero ¿Cómo evaluar que medidas de seguridad usar?
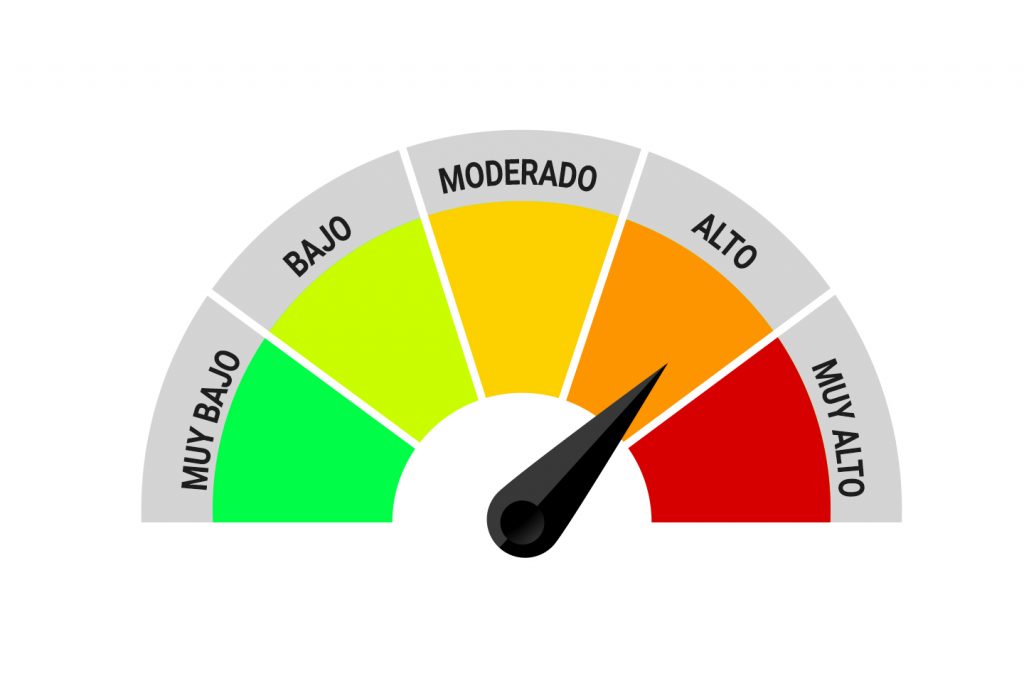
Análisis de riesgos.
El análisis de riesgo es básicamente la respuesta a muchas interrogantes para evaluar medidas de seguridad y así evitarse en su mayoría la ocurrencia de incidentes, como prevenir incidentes mayores y poder tener una respuesta rápida cuando ocurra.
Hay varias formas de realizar esto, tales como:
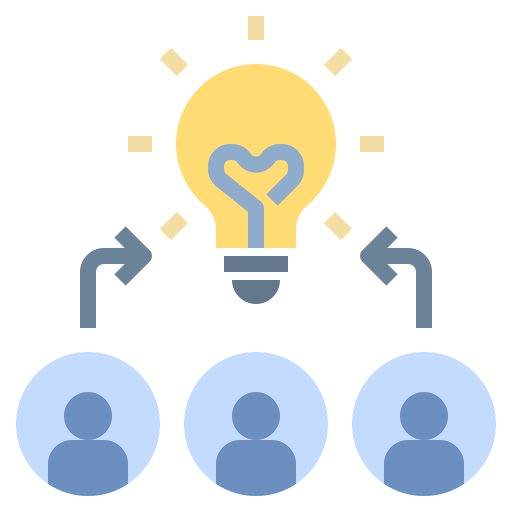
Brainstorming.
En una junta de las partes de la empresa quienes supervisan o están a cargo de las áreas, donde estos indiquen los problemas y errores cometidos por los empleados al momento de realizar sus actividades que causan problemas o pueden causar problemas en una falla, descuido o previsión futura por desgaste ya captado, a través del brainstorming se manifiestan los problemas posibles que estarán surgiendo y pueden ser en ese momento tratados para implementar normas, manuales, capacitaciones, dispositivos, advertencias, equipo de protección, todo con el fin de evitar los accidentes.
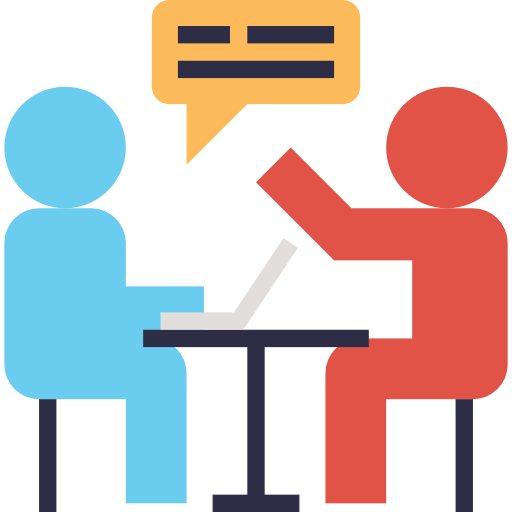
Cuestionario y entrevistas estructuradas.
Tal vez hacer un brainstorming lleve a una junta larga que consume tiempo valioso que los miembros principales del equipo no puedan participar, por lo cual si falta uno no se podría tomar en cuenta sus datos, para ello se puede en su lugar o en combinación con el método anterior para generar una herramienta que genere una lista y datos concretos, a través de un cuestionario estructurado, con las preguntas clave, específicas y que ofrezcan las opciones que pueden ser reveladoras en cuanto a problemas y situaciones de riesgo que se han presentado, sofocadas por el supervisor o gerente al percatarse, pero pueden ser eliminadas de raíz o mejor tratadas.
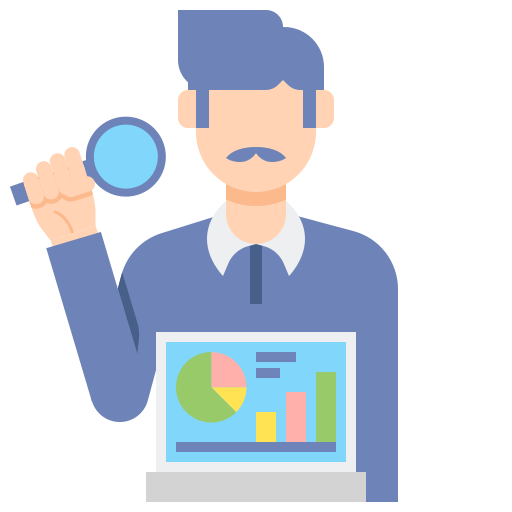
Juicio de especialistas y expertos.
Cuando el personal no tiene cómo dar reporte o no saben debido a que son nuevos o en ningún momento les ha pasado hasta la fecha ningún incidente, la capacidad de prever estos problemas o incluso de figurar mentalmente algún accidente puede ser nula, contando con ceguera de taller, pero el riesgo existe y cuando ocurra el incidente el equipo puede no estar preparado el equipo, para ello se opta por un juicio de especialistas y expertos, esto es consultar a personal de otras empresas, consultores o expertos en las mismas áreas participen solo en el desarrollo del análisis de riesgos, para identificar estos problemas que el equipo actual no puede dilucidar, estos pueden desarrollar un documento con los factores a tomar en cuenta, situaciones, riesgos y cómo prevenirlos.
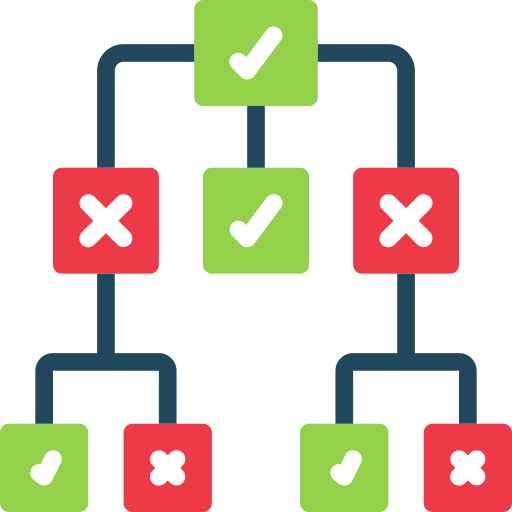
Análisis what if (¿qué pasaría si…?)
El análisis what if, especula situaciones, escenarios que pueden desarrollarse en el entorno laboral, formas de ver las actividades de inicio a fin, manipulación de maquinaria y poner en situación de problemas, que pasaría si la válvula no cierra, qué pasaría si el piso está resbaloso, qué pasaría si se cae tal pieza, qué pasaría si se excede tal temperatura en la máquina, entre otros escenarios que permiten ver como prevenir los incidentes.
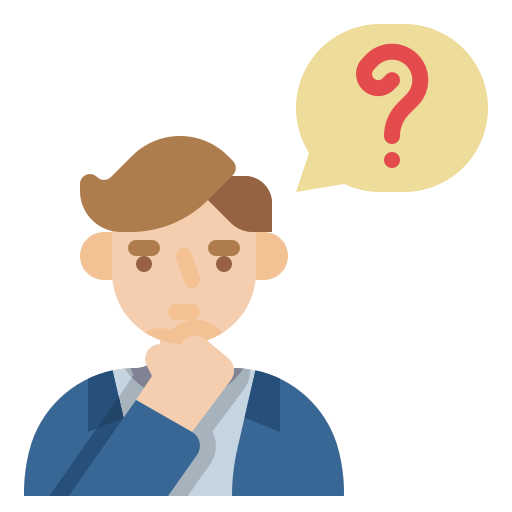
5 porqués
Cuando los problemas ya están ocurriendo constantemente, esto puede causar un efecto adverso en el rendimiento operativo, financiero y muchos otros factores, por ello es necesario descubrir la causa raíz del problema, por causa raíz nos referimos al origen de la causa del problema, por ejemplo si una válvula esta rota, ¿bastará cambiar la válvula para que no ocurran más estos problemas? Puede que ya se haya hecho esto antes y volvió a ocurrir el problema, se volvió a romper la válvula, eso quiere decir que no es la raíz del problema, más bien es un problema más serio que hay que descubrir por qué ocurre.
Este método justamente nos ayuda a desvelar estas causas raíz, para ello al igual que niños que preguntan porque a todo, debemos de hacer pregunta tras pregunta, hasta encontrar la verdadera causa, ¿Por qué la válvula se rompió? Porque el flujo de vapor es de alta temperatura y desgasta el material ¿Por qué es de alta temperatura?… Así una y otra vez hasta descubrir el dilema, por ejemplo podemos concluir que la tubería instalada no es la correcta para tanta densidad de vapor usado en el proceso, lo que ocasiona que la válvula se rompa y deje escapar vapor a altas temperaturas que dañan a los operarios, por lo que si cambiamos la tubería por una de mayor capacidad, debería dar por finalizado este problema y mejorar el rendimiento.
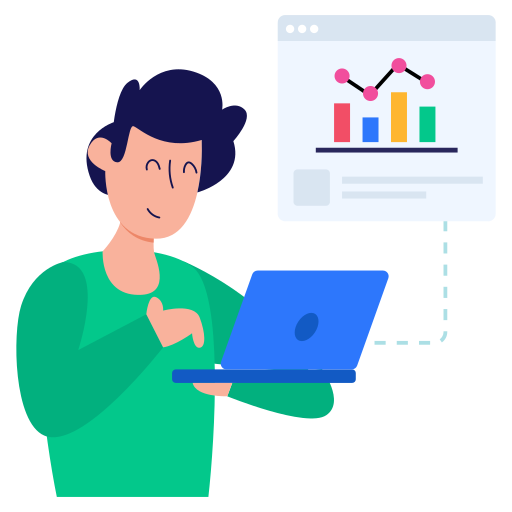
Análisis preliminar de riesgos (APR)
Esta metodología de análisis de riesgos involucra tener bien planificado el proyecto operativo que se realizará, ya que sus fases empiezan tomando en cuenta el diagrama de flujo de actividades a realizarse para el proceso productivo que se desempeñará o para todos los procesos, es decir todos los diagramas de flujo que involucren los procesos productivos.
Posteriormente se genera una tabla de registro de 4 columnas, en la primer columna escribiremos los riesgos identificados dentro del diagrama de flujo, en la segunda columna colocaremos las posibles causas que pueden llevar a incidencias, en la tercer columna detallaremos las consecuencias de no tratar estos riesgos a tiempo y finalmente en la última columna crearemos un mix entre frecuencia y gravedad del riesgo percibido, es decir si el riesgo se puede presentar seguido y es mortal o es cada año y el riesgo es menor es decir heridas leves, ayudando a crear una clasificación de riesgos y prioridades, esto tomando en consideración maquinarias y materiales que con el paso del tiempo se degradan y pierden su eficacia, logrando deteriorarse hasta el punto de romperse y necesitar ser cambiados.
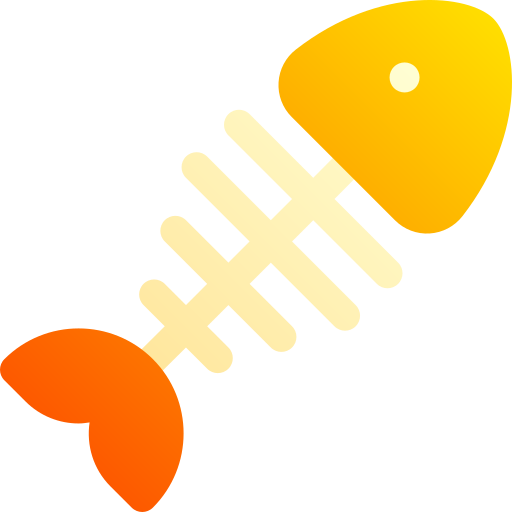
La “Espina de pescado” de Ishikawa
Este método es muy similar al de los 5 porqués y el análisis preliminar de riesgos, fue un método creado por el ingeniero japonés llamado Kauru Ishikawa.
Su método consiste en un diagrama similar las raspas o espina del pescado, tener un eje central en horizontal y vertientes inclinadas que van arriba y abajo que dictaminan las áreas o procesos productivos, como lo era en el análisis de riesgos, pero aquí vistos en un solo diagrama, ahora dentro de cada vertiente sacamos una espina en horizontal donde colocamos qué posibles fallas tenemos y de estas fallas sacamos nuevas vertientes con sus posibles soluciones, es decir vamos explorando una a una como una rama de árbol diferentes causas, sus soluciones y su forma de que estos encaminen una solución final entre todas las ramas, sea resultado de diferentes soluciones o bien algunas soluciones que solucionen que cubran todos los problemas, similar al método de los 5 porque donde veníamos explorando en cada pregunta si solucionaba de raíz el problema o si este se estaba aún desplazando más con problema tras problema.
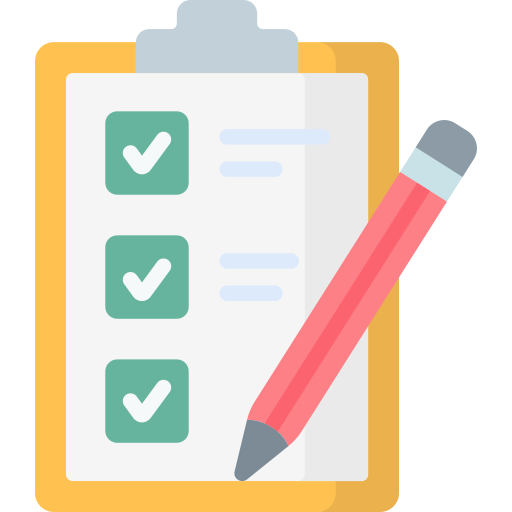
Lista de chequeo.
Finalmente tenemos esta metodología simple, útil y que se puede usar en conjunto con los anteriores como conclusión e implementación en los procesos de supervisión constantes que se deben entregar a gerencia y directivos, este método consiste en crear una lista de los factores detectados que deben procurarse contar como bien provistos o en buen estado, por ejemplo verificar en cada empleado esté con su equipo de protección puesto, si todos lo llevan correctamente es una palomita en la lista de chequeo, si falta uno, hay un fallo, si se realiza un mantenimiento determinado por ciclo de tiempo, periódico cada x meses, es parte de una lista de chequeo para evitar accidentes futuros, si no se realiza dicho mantenimiento no se puede palomear de la lista de chequeo semestral o anual de cosas por tener que hacer, así entre todas las verificaciones necesarias, pisos secos, guantes en óptimas condiciones, señalética correcta, temperaturas en el marcado correcto, presión correcta, etc.
Todo detalle necesario que agregue valor en base a las metodologías anteriores o que se detecten sean necesarias para evitar un accidente.
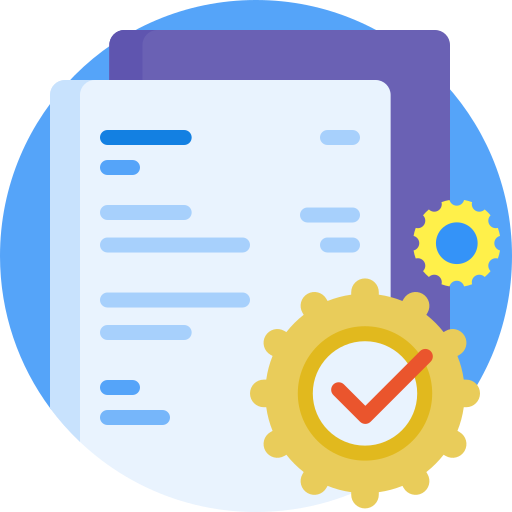
Conclusión.
Con estos métodos de análisis de riesgos, se podrá contar con un sistema más eficiente de prevención de problemas y a su vez idealizar respuestas para mitigar problemas más severos que pueden afectar financieramente a la empresa, estar preparado para reacción, control y minimizar los riesgos, es una forma exponencial de ahorro en costos, ante pagos de indemnizaciones, juicios por seguros, ausencia de personal, demandas por accidentes, entre otros casos que pueden acabar en gastos desmesurados de pagos no contemplados, merman las ganancias, las consumen y finalmente causan estragos en la empresa, contar con el análisis de riesgo evitará todo eso y lo minimizará.